Pilotless Helicopters Deliver Large Payloads with Precision
Autonomous Helicopter Startup Tests Prototype for Drone Deliveries
Global supply chains are in crisis. More than ever before, goods are procured with the click of a mouse and delivered to a specific address, often in short order, requiring a sophisticated supply chain with many moving parts. With double-digit e-commerce growth and a global labor shortage, stress comes from varying points along the supply chain: unloading items from ships at ports, sending materials to warehouses, and finally, dispersing parcels to local delivery centers. All play a critical role in this new world of logistics for shorter distances.
Solving the logistics issue requires new technology, from small robots cruising along sidewalks for last-mile deliveries to large aerial cargo vehicles that can move heavier items earlier in the supply chain. RangeAero, a startup from Bengaluru, India, is taking to the air to help alleviate the issues in heavy payload logistics for shorter distances.
Imagine an uncrewed aircraft soaring through the air with a 100-kilogram (220-pound) package, descending, and delivering the materials from suppliers to the assembly line with great precision and speed. RangeAero has developed a vertical takeoff and landing (VTOL) aircraft that makes such a delivery possible.

The RangeAero pilotless helicopter delivering a shipment. (Image credit: RangeAero)
Precise Vertical Takeoff and Landing
RangeAero’s sleek coaxial helicopter differs from conventional helicopters in that it has concentric rotors, one above the other, which rotate in opposite directions. The blades change their pitch to control the locomotion.
The coaxial design gives it vertical takeoff and landing capability while minimizing the footprint of the helicopter. Unlike conventional helicopters with a single rotor above the fuselage and tail rotor to counter the rotor’s torque, a coaxial helicopter maintains stability without the extra length required for a tail rotor assembly. This type of helicopter is better suited to logistics systems and infrastructure where landing and takeoff space is limited and precise delivery is required.
“Coaxial helicopters are agile and can land in a very congested space. The coaxial rotor configuration affords extraordinary capability in carrying cargo and is stable in extreme weather.”
“Coaxial helicopters are agile and can land in a very congested space,” says Arpit Sharma, co-founder and CEO of RangeAero. “The coaxial rotor configuration affords extraordinary capability in carrying cargo and is stable in extreme weather.”
The rotors of a coaxial helicopter are larger than those of a quadcopter, which uses four small rotors to generate lift. Quadcopters or multi-rotors are advantageous because they are easy-to-use vehicles, are modular, and have fewer rotating parts. However, they lack efficiency, flight capability, and airworthiness safety in smaller landing and takeoff footprints.
“Warehouses near urban areas with congested space benefit from B2B deliveries,” adds Sharma. “When operating in these areas, safety and efficiency are key.”
The RangeAero team flies a prototype of their autonomous helicopter. (Video credit: RangeAero)
Accelerating System Development
RangeAero approached the design and development of the coaxial helicopter using a systems engineering approach common in the design of larger complex aircraft. “Our development team specifically follows NASA’s systems engineering approach,” says Sharma. “This requires developing the craft through various levels of prototyping, where each prototype is an engineering product made to meet certain objectives.”
The technology’s development journey began with the accelerator, Forge. Forge partnered with the MathWorks Accelerator Program, enabling its startups to leverage Model-Based Design and technical computing tools, including MATLAB® and Simulink®. MathWorks also provides the accelerator members technical support and mentoring.
The aircraft’s design and development team are versed in aerospace systems engineering and prototype development. Their initial challenge was to validate the theoretical design decisions. The team developed a testing methodology based on scaled prototypes. They projected the next design iteration of a larger scale aircraft from the prototype stage. The simulations were completed in Simulink.
“In a coaxial helicopter, the rotor flow interacting with the other rotor is highly complex and affects the dynamics of the helicopter,” says Rohit Gupta, co-founder and CTO of RangeAero. “MATLAB and Simulink modeled the vehicle dynamics based on the theoretical hypotheses. We then validated the test results. For a quick interpretation of the analysis, we have developed workflows using Model-Based Design, including analyzing flight data, systems health data, and the communication logs of every flight. Overall, it helps improve the design fast and frequently.”
“We have developed workflows using Model-Based Design, including analyzing flight data, systems health data, and the communication logs of every flight. Overall, it helps improve the design fast and frequently.”
Designing Within a Complex Ecosystem
“RangeAero focuses on developing the end-to-end ecosystem required for such operations,” Sharma says. “We develop and manufacture the aircraft. We will then operate a drone port with a command-and-control center analogous to air traffic control. Ultimately, we will be a cargo airline.”
“When we are developing the brain of the aircraft, including things like control systems and other integrated systems, we used MATLAB intensively,” Gupta states. “We wanted to develop rapidly, test it, and deploy it.”
Simulation in Simulink is key to development. Simulation is safe, less costly, and forgiving. It provides the RangeAero development team ample opportunity to refine designs, apply different specifications, accurately test their prototypes, and validate the overall design.
Simulation in Simulink is key to development. Simulation is safe, less costly, and forgiving. It provides the RangeAero development team ample opportunity to refine designs, apply different specifications, accurately test their prototypes, and validate the overall design.
“In developing a new product, having a systems engineering–based decision approach helps generate confidence when demonstrating the concept to an audience,” says Gupta. “Making the right projections and simulating the performance in various use cases were key factors that helped achieve product success.”
Gupta also credits the applications engineering team at MathWorks with prompt and helpful assistance to his team.
“The RangeAero technical team worked together with the applications engineering team at MathWorks to learn to use the tools and apply them to our complex applications,” says Gupta. “The team from MathWorks was always a call away when we needed help regarding the toolboxes required in setting up workflows.”
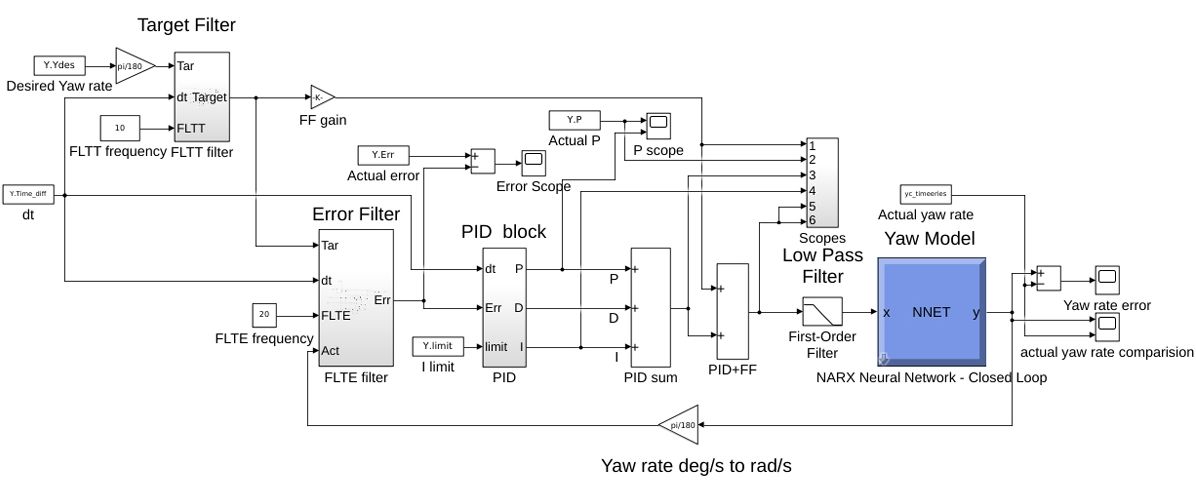
Deep learning–based Yaw Controller implemented in Simulink. (Image credit: RangeAero)
The RangeAero development team has conducted more than 100 test flights of their prototype and continues to develop the coaxial helicopter with different ranges and payload capabilities. Their goal is to successfully move 100 kg for 80 kilometers (50 miles) with their signature coaxial helicopter, Range100, a microlight helicopter weighing 223 kg (492 lbs.), without fuel and payload. Its longest dimension is 7 meters (23 feet) in width, the diameter of the rotor motion path, and it can carry 100 kg for 200 km (124 miles) for two to three hours.
“We have developed the scaled versions of this as the Range5 and Range10 with payload carrying capacities of 5 kg (11 lbs.) and 10 kg (22 lbs.), respectively,” says Sharma. “These scaled versions help us validate the technologies involved and the deployment strategy of a hub-and-spoke model for logistics clusters.” Hub-and-spoke models are logistical configurations used to efficiently manage the movement of payloads in a transportation system.
One of the major operational challenges was designing the craft within a specified ecosystem that could precisely approach and land on the landing pad. After analyzing different approaches to data perception and a subsequent ability to make decisions quickly, the team decided to utilize a vision-based system, further reducing hardware requirements. Image processing also works well with sensor fusion, coordinating with the other sensors involved in the flight.
Operating in a Complex and Controlled Environment
“Currently, the regulatory environment is gaining momentum to include unmanned aircraft; however, the pace of the introduction of regulations varies by geography,” says Sharma. “We are developing the aircraft according to design standards laid out by the European Union Aviation Safety Agency, which is responsible for defining certification standards and airworthiness and safety directives. Our aircraft and delivery ecosystem fall under Type 1 and Type 2 categories of certification.”
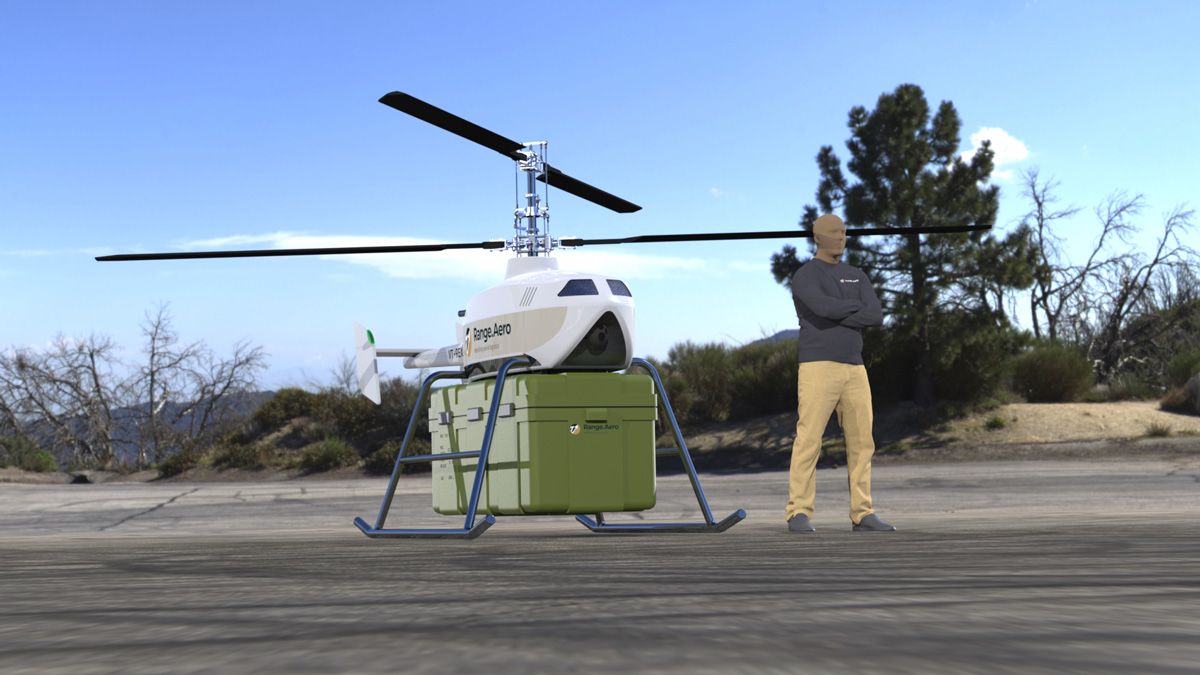
The RangeAero helicopter. (Image credit: RangeAero)
These categories are for aircraft flying in certain classes of airspace with instrument flight rules (IFR). Flights interacting with air traffic control operate under IFR when the cloud ceiling is less than 305 m (1,000 ft) above ground level, or visibility is less than 4.8 km (three miles).
“Soon, we will look to expand to cargo flights from dedicated drone ports in predefined drone corridors, both in India and abroad,” says Sharma.
A key benefit afforded by MATLAB and Simulink was the “what if” scenarios of flight the team could apply and the help such tools provided them in correcting deficiencies or weaknesses in their designs.
“Understanding how your system responds to the practical environment and provides feedback for the corrective measures to the design team helped speed up the design process,” says Sharma.
The interaction between the onboard systems and the command-and-control center is vital.
“We achieved this using predictive maintenance techniques and a health diagnostics system, which broadcasts the real-time health data of the subsystems involved in the vehicle to the command-and-control center,” says Sharma. “This was built using MATLAB toolboxes and a core codebase that we developed in the previous three years.”
RangeAero is transforming aerial logistics with the right tools, the right approach, and the right team, demonstrating the viability of an unmanned helicopter to connect industrial hubs, delivering goods safely and on time.
“Leveraging the right technology support is crucial to building the right product and building the product right,” says Vish Sahasranamam, co-founder and CEO of Forge. “At Forge, we enable this capability through partnerships with leading technology players. The partnership with MathWorks has enabled our startups to leverage industry-standard tools such as MATLAB and Simulink.”
For the RangeAero team, their mission to redefine and disrupt the logistics technology with their helicopter continues as they work to unveil new possibilities for the global supply chain.
Read Other Stories
AI / ROBOTICS
Self-Driving Trucks Could Alleviate Supply Chain Problems
Computer Modeling Helps Build the Future of Autonomous Semi Trucks
AI / ROBOTICS
Autonomous Electric Tractor Brings Artificial Intelligence to the Field
California Vineyard Finds Driver-Optional Smart Vehicle Has Power to Spare
IMAGE PROCESSING / STARTUPS
Seeing the Road Ahead
The Path Toward Fully Autonomous, Self-Driving Cars Cars