Airbus Defence and Space Achieves Civil Certification with DO-254 (DAL A) FPGAs Using Model-Based Design
“The key challenge for achieving certification for flight control avionics has been applying rigor to find errors during the earliest requirements phase while taking benefits from HDL code generation and verification reusing.”
Key Outcomes
- Large teams enabled to work in the same architecture by using referenced models
- Simulink toolboxes tailored to the ED-80/DO-254–compliant Airbus ALM development process
- Automatically generated HDL code developed for ED-80/DO-254
- Quality HDL code with full hardware verification that allowed designers to focus on hardware functionality
- Errors detected by reusing tests at different integration levels
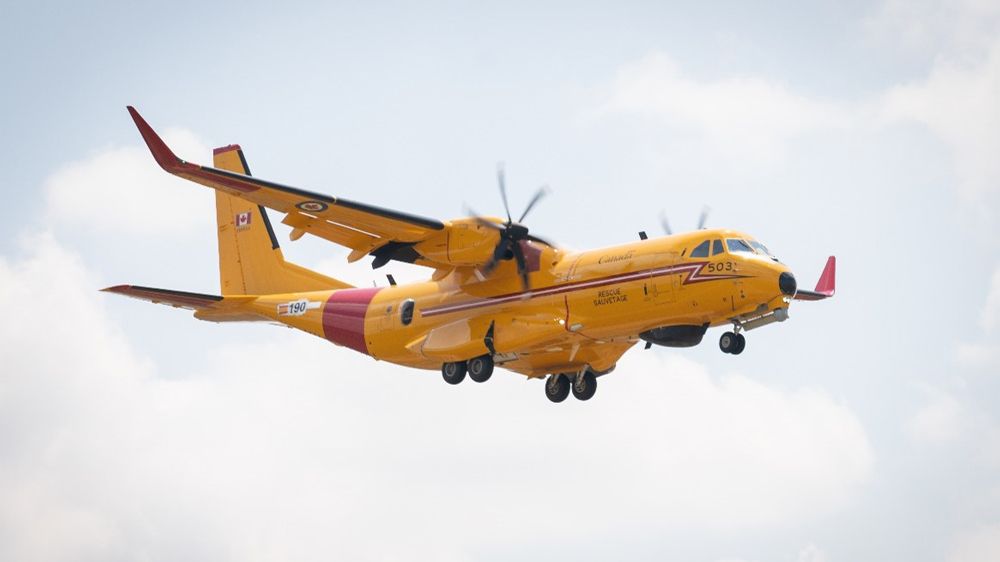
The Airborne Electronic Hardware (AEH) group within Airbus Defence and Space has developed a flaps high lift control unit (HLCU) for Airbus C295 aircrafts with civil certification of airborne hardware according to EASA EUROCAE ED-80/FAA RTCA DO-254 and EASA certification memo SWCEH-001.
The HLCU embeds all of its complex hardware functionality in FPGAs. MATLAB® and Simulink® enable key process adherence by reducing the design and test phases, leading to safer hardware development. Using MATLAB and Simulink helped the AEH group complete the full V-model cycle: modeling, simulation, automatic HDL code generation, testing, and verification for the HLCU. At the beginning of 2020, the AEH group achieved the world’s first ED-80/DO-254 safety-critical civil certification with EASA and FAA using this workflow, Model-Based Design, and HDL code generation.
Products Used
Related Resources