What Is a Battery Thermal Management System?
A battery thermal management system keeps batteries operating safely and efficiently by regulating their temperature conditions. High battery temperatures can accelerate battery aging and pose safety risks, whereas low temperatures can lead to decreased battery capacity and weaker charging/discharging performance.
A battery thermal management system controls the operating temperature of the battery by either dissipating heat when it is too hot or providing heat when it is too cold. Engineers use active, passive, or hybrid heat transfer solutions to modulate battery temperature in these systems. Active solutions typically have a fan or pump pushing working fluid—such as air, water, or some other liquid—to reduce or increase battery temperature. In a passive solution, either heat sinks or pipes with thermally conductive materials transfer heat away from the battery. A hybrid solution combines key design features of both active and passive solutions.
Creating battery thermal software models that simulate the heat transfer process can help engineers analyze tradeoffs in design parameters, evaluate performance, and implement control algorithms. Engineers can use MATLAB® and Simulink® to design battery thermal management systems that ensure a battery pack delivers optimal performance safely in a variety of operating conditions.
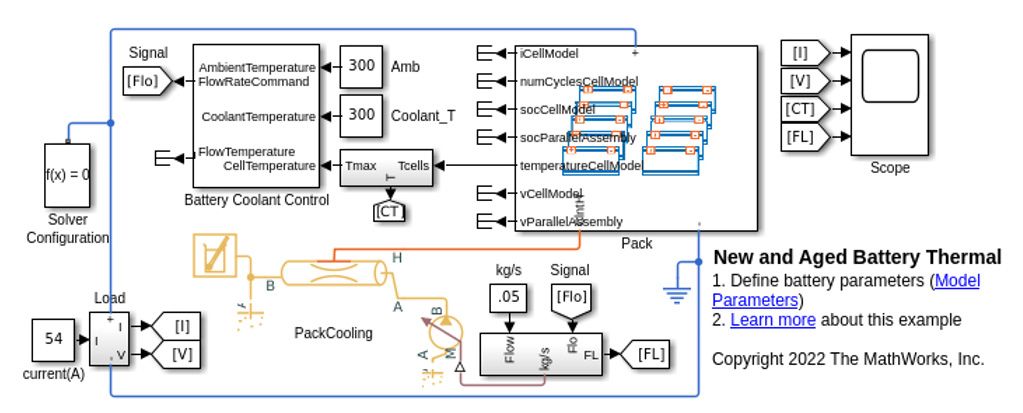
Conduct thermal analysis in Simulink on a new and an aged lithium-ion battery pack model to design battery packs that meet warranty criteria at end-of-life (EOL) time from power, performance, and packaging perspectives.
With MATLAB and Simulink, you can:
- Model detailed thermal behavior of the battery
- Build models for cooling/heating systems using various working fluids, including gases, liquids, and refrigerants that change phase
- Perform component selection and component sizing with modeling and simulation
- Explore the design space with different component parameters and optimize battery thermal management system performance
- Simulate extreme temperature conditions to design for “what-if” scenarios
- Design supervisory control logic and closed-loop control strategies for temperature modulation
- Conduct scenario studies to assess the thermal impact of different design options
- Reduce costs by performing fewer expensive, time-consuming tests with production battery hardware
- Automatically generate production-ready embedded code for battery thermal management controls and qualify against industry standards
Capture Battery Thermal Behavior
Using Simscape™ and Simscape Battery™, you can create models starting at the battery cell level and then add ambient temperature effects, thermal interface materials, and cooling plate connections to create a more representative model. Heat transfer can be considered from cell-to-cell, cell-to-plate, and cell-to-environment perspectives by defining the thermal paths to the ambient, the coolant, and the location of the cooling plate. Simscape Battery provides pre-built cooling plate blocks that support different flow configurations, including parallel channels, U-shaped rectangular channels, and edge cooling.

Parallel channels block in Simscape Battery
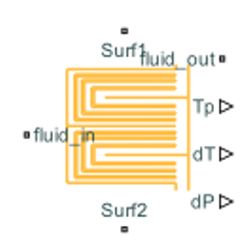
U-shaped channels block in Simscape Battery
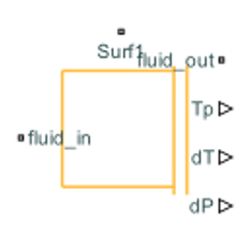
Edge Cooling block in Simscape Battery
Temperature spreads resulting from the dynamic interaction between the battery and coolant flow can be closely captured by discretizing these cooling plates into elements.
A pack-level thermal model can be built by assembling cells into modules with thermal effects and arranging modules inside a pack. Battery pack models built in Simscape use electrical and thermal networks which mirror the actual system and scales as the number of cells increases. You can perform thermal performance analysis on battery packs with different levels of aging to meet warranty criteria at end-of-life (EOL) time.
Model Cooling/Heating Systems
You can use Simscape and Simscape Fluids™ blocks in gas, liquid, and thermal domains to model active, passive, or hybrid cooling/heating solutions. You can also explore cooling/heating system architectures by drawing schematics to place pipes, valves, heat exchangers, and tanks. In the case of a liquid loop system, you can model an expansion tank that keeps reserve fluid; cold plates that channel the working fluid near the battery cells; a motor-driven circulation system with the pump, flow path, and valves; and different types of heat exchangers such as wired heaters or radiators. After you have created a model of the cooling/heating system, you can run simulations, refine the design by exploring component sizing and system parameters, and satisfy requirements such as heat dissipation and power consumption.
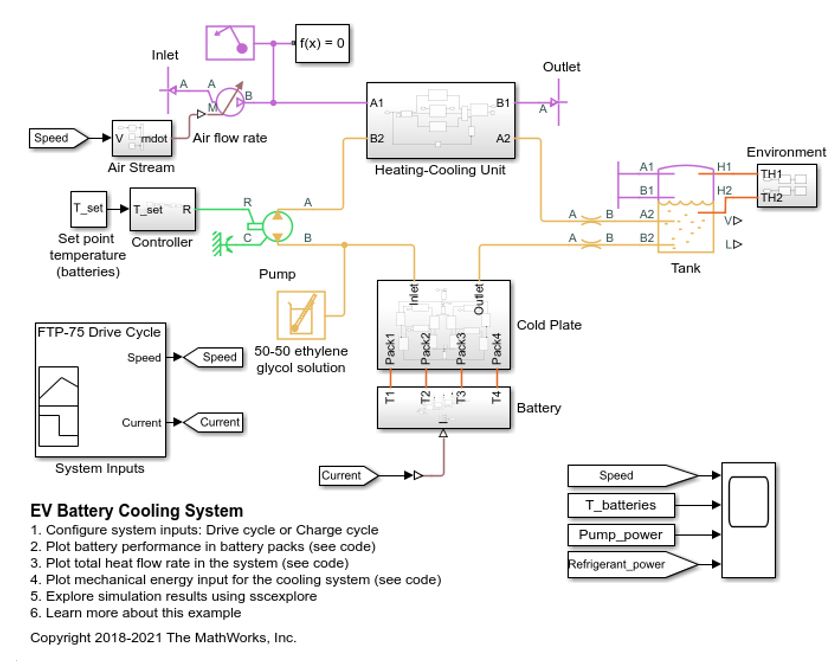
An active liquid-loop cooling/heating system model for batteries in an electric vehicle (EV) created using Simulink and Simscape
Design Controls for Battery Thermal Management
Simulink makes it easy to design closed-loop controls that combine feedforward and PID techniques for circulation system controls—such as feed stream (valve) control, mass flow (pump) control, and heat exchange path selection control. With Simscape Battery, you can use pre-built blocks, such as battery coolant control and battery heater control, to build battery thermal management control algorithms. With Stateflow, you can also design supervisory control logic for switching between different operating modes—such as heating versus cooling—based on the environmental temperature and the battery temperature.
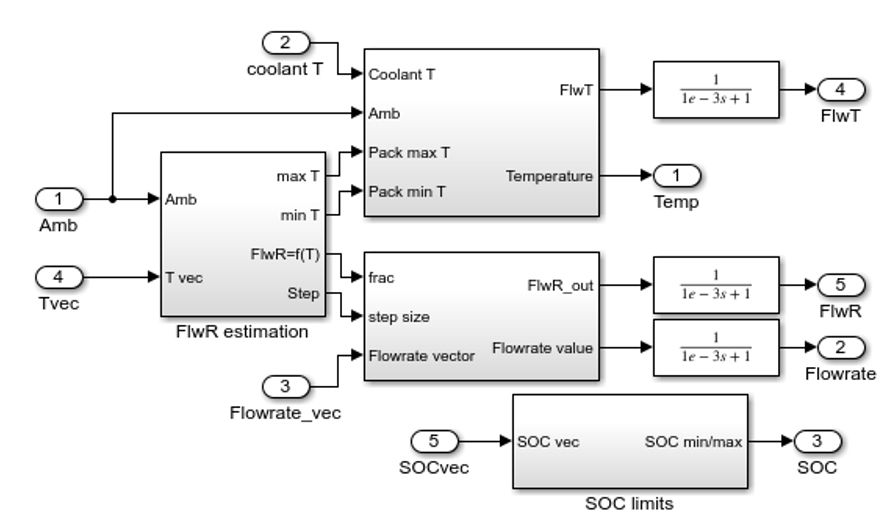
A Simulink model of a coolant control system that calculates the flow rate based on temperatures among the battery cells as well as the ambient temperature
Generate Code and Perform Hardware-in-the-Loop (HIL) Testing
With Embedded Coder® and HDL Coder™, you can automatically generate readable, optimized C/C++ or HDL code for deploying your battery thermal management system software on embedded microcontrollers or FPGA/SOC targets. You can also generate the code for the plant model and perform hardware-in-the-loop (HIL) testing. Simscape Battery includes blocks that act as interfaces between the battery and the cell supervisory circuit. Using these blocks with real-time hardware, you can connect your battery simulations to real-world battery balancing hardware. HIL testing of battery systems enables you to replace time-consuming and expensive hardware tests with a real-time machine to test the battery thermal management system. This reduces the risk of damaging the battery hardware in potentially dangerous testing conditions, allowing you to test the battery thermal management system under a wide range of operating conditions including extreme temperatures, degraded operations, and faults.
Examples and How To
Simscape Battery Examples
Simscape Electrical and Simscape Fluids Examples
Videos
Customer Stories
Software Reference
See also: battery models, battery management system, battery state of charge, simulation software, modeling and simulation, Simulink for Electrification, PID tuning, battery pack design